Get to know LumosAX through a collection of visual representations of its capabilities!
LumosAX is designed to provide an extensive level of detail for each evaluation phase; however, the information presented here offers a concise yet insightful high-level overview of LumosAX's capabilities.

Phase 1
Demonstration of LumosAX's Feasibility Evaluation System -
LumosAX's advanced feasibility analysis provides direct guidance about the AM readiness of parts from a comprehensive technical and economic perspective and eliminates biases and inconsistencies in decision-making for additive manufacturing the parts.

Four Sample Parts
LumosAX's feasibility system accurately identifies the non-printable regions in the parts and also scores the desirability of their geometry for printing.
The blue and red regions indicate seven distinct problematic features for printing.
LumosAX's feasibility system has identified the geometries of all sample parts as falling under the "Unacceptable" level, with each part exhibiting multiple problematic features.

LumosAX identifies the optimum build orientation for support generation and scores the desirability of support consumption for manufacturing the parts.
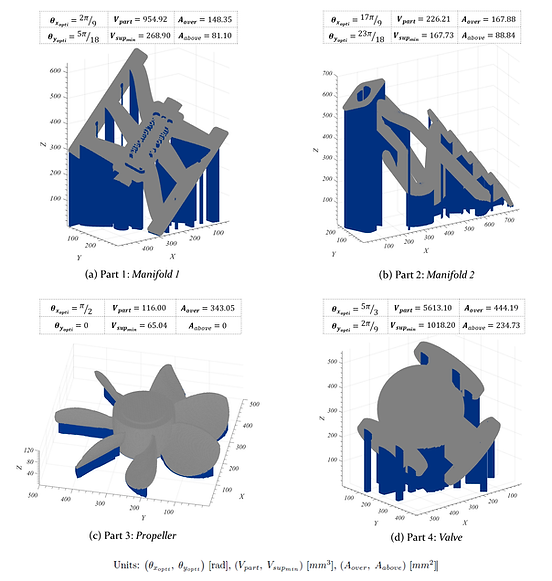
In addition to the optimum build orientation, LumosAX also inform users about critical features related to support structures, including internal supports for inaccessible areas, the fraction of internal support to total support volume, and overhang areas.
LumosAX has determined the feasibility levels for the support of Part 1 and Part 2 as "Tolerable" and "Undesirable," respectively, while Part 3 and Part 4 are estimated to fall within the "Desirable" feasibility level.
LumosAX's intelligent scoring system utilizes the extracted feasibility data to generate feasibility graphs for the six soft assessments.


The graphs provide insights into the suitability of each sample part for AM from various technical and economic perspectives.
LumosAX defines the best and worst scores as 0 and 10, respectively, representing the "Ideal" and "Unacceptable" feasibility levels. LumosAX implements a nonlinear scoring method to ensure the highest accuracy in computing the part's feasibility, and it pioneers a flexible feasibility space for AM readiness computations, ranging from "Ideal" to "Unacceptable".
By utilizing this precise and science-based scores, LumosAX eliminates biases and inconsistencies in decision-making for AM.

Phase 2
Demonstration of LumosAX's Geometric Correction System -
LumosAX's correction system applies the necessary design corrections to infeasible parts and converts them into reliable and feasible parts geometry through a fully automated process with minimal user interaction.

CAD Models of Six Sample Parts
LumosAX's geometric detection algorithm first identifies the unprintable problematic areas in sample parts.

LumosAX's correction system then modifies the geometry of infeasible parts with minimal design changes through an automated three-step process.
LumosAX generates a graphical output after each step to visually indicate the modified regions to the user.

Real-life case comparisons of 3D-printed parts before and after LumosAX's modifications.

The original models of the sample parts (Fig (a)) included numerous regions that posed challenges for 3D printing, leading to wasted resources and limited value. However, LumosAX's correction system ensures promising and reliable 3D-printed parts (Fig (b)).

Demonstration of LumosAX's Recommender System -
Phase 3
LumosAX's intelligent recommender system has been developed based on a machine learning algorithm to efficiently manage a large inventory of components (ranging from thousands to millions of parts) and optimize resource utilization in an organized and systematic manner.

LumosAX's recommender system conducted an advanced and systematic evaluation of a database consisting of 645 diverse parts.
This figure include data for 11 out of the 645 parts .
LumosAX's recommender system effectively classifies and manages sample parts into four distinct and meaningful clusters.

A selection of 15 sample parts from each four cluster is represented here. These groups are distinguished based on their desirability in terms of geometry and resource consumption.
In cases where infeasible part clusters are detected, LumosAX offers unique design and resource modifications. This enables the conversion of these parts into additive manufacturing (AM) feasible parts in a highly efficient manner. This classification process helps streamline and expedite the transition to additive manufacturing.